In the highly competitive manufacturing industry, production managers are constantly looking for ways to increase efficiency and reduce costs. Robotic welding is very rewarding, but it is time-consuming and expensive if not done correctly.
We have developed several different software functions for the collaborative welding robot CoWelder which improve the welding process. They also make you able to customise your CoWelder solution to your needs.
That’s where welding seam tracking comes in.
It is the process of following the seam along the joint during arc welding to ensure that it’s done accurately and consistently.
Table of Contents
Seam Tracking for Cobots
Cobots and seam tracking technology are a great match. Through arc seam tracking, the cobot can maintain a consistent welding path, while the cobot’s precision and accuracy ensure that the welds are completed with maximum efficiency.
In addition, the cobot’s ability to work tirelessly and without fatigue means that it can maintain a consistent speed and angle for long periods, resulting in welds that are both accurate and uniform.
Overall, the combination of cobots and seam tracking technology is a game-changer for production managers looking to improve their welding processes.
By automating the process and ensuring greater accuracy, this technology can help to reduce the risk of defects and rework, resulting in higher quality finished products and increased profitability for your business.
So, if you’re looking to take your welding processes to the next level, be sure to consider cobots and seam tracking technology as an essential tool in your production arsenal.
In this blog post, we’ll explore the benefits of seam tracking for CoWelder and why it’s a competitive key in the field of cobot welding.
What is Seam Tracking?
Seam tracking is a software functions that improves weld quality by making instant, real time adjustments to the weld seam. It adjusts the weld path based on the workpiece’s shape and position and automatically correct for slight deviations or variations in the welded item during welding. This means that even if the workpiece is not perfectly aligned, the cobot can still produce a high-quality weld.
What are the advantages of using Seam Tracking for CoWelder?
The technology, when integrated with collaborative welding robots like CoWelder, offers a range of advantages that make it a competitive key for production manufacturers.
It measures the arc, while weaving and maintating a consistent position in the centre of the weld joint. It maintain a consistent distance and angle from the seam, ensuring high precision and accuracy in the welding process.
By enabling cobots to maintain a consistent welding path with precision and accuracy, you can ensure that welds are completed efficiently and to the desired quality standards.
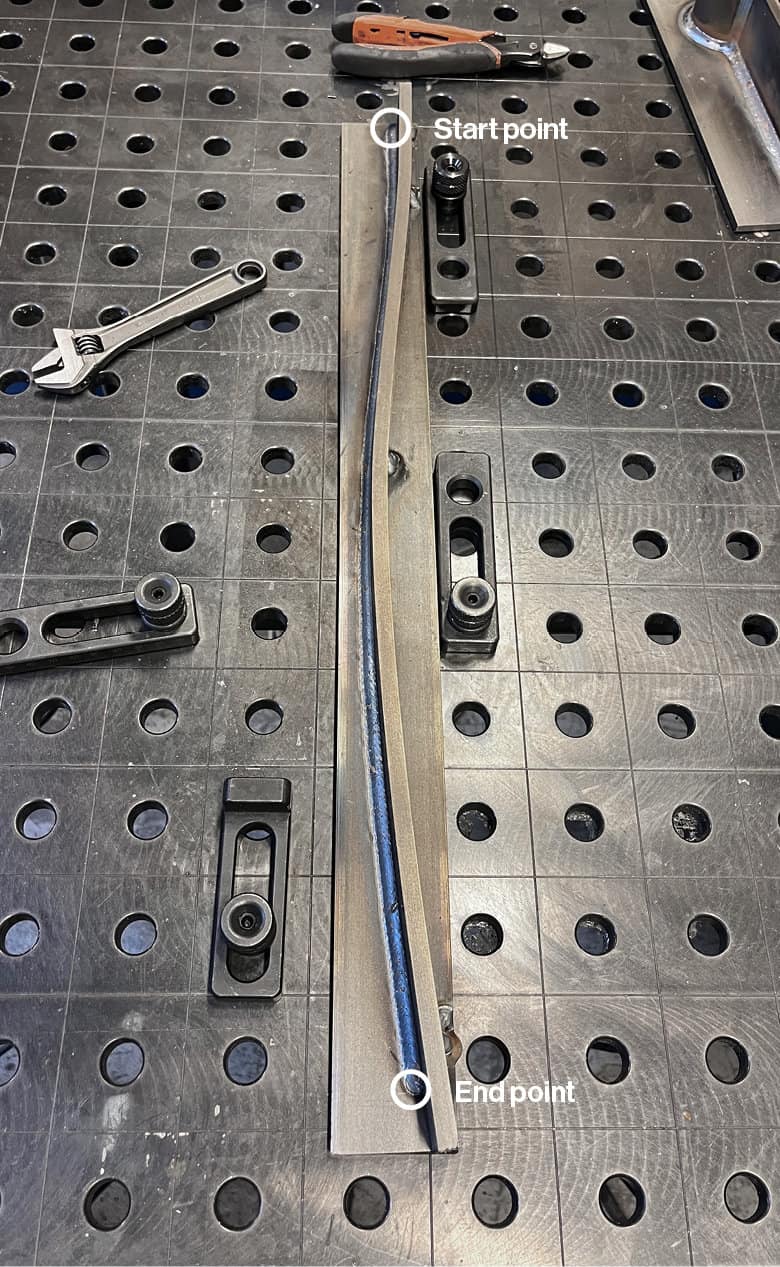
With just one start point and one end point, it was possible to weld this item even with deviation up to approximately 70 mm over the total distance of 600 mm.
35 mm outward, followed by 35 mm inward to the same reference point.
Material thickness: 10 mm.
Here are some benefits you can achieve when using seam tracking:
1. Accuracy
Seam finding helps to improve the quality of the weld. The CoWelder can detect any deviations or irregularities in the seam, such as gaps or misalignments and move the position of the torch accordingly. The result is a high-quality weld that meets the required specifications and standards.
2. Improved weld quality
With precise positioning, it becomes possible to weld your items with uniform accuracy every time. The result is a high quality finished product. You don’t have to worry about inconsistency in your welded items.
3. Improved welding process
Get a more reliable process. Eliminate the guesswork and human error that often lead to quality concerns and rework. It ensures that your welding cobot applies the weld exactly where it’s needed, resulting in a flawless and uniform finish. This leads to a significant improvement in your weld quality, reducing the risk of product failures or defects. With superior weld quality, you can deliver better products to your customers, improving your brand reputation and customer satisfaction.
4. Reduces the need for rework
You can eliminate the need for manual intervention in terms of rework and the associated costs, which can quickly add up over time. This can lead to costly rework and production delays.
5. Easy programming
The user-friendly interface enables easy set-up and customisation if necessary.
Statement:
“The robot can only do what you tell it to do”
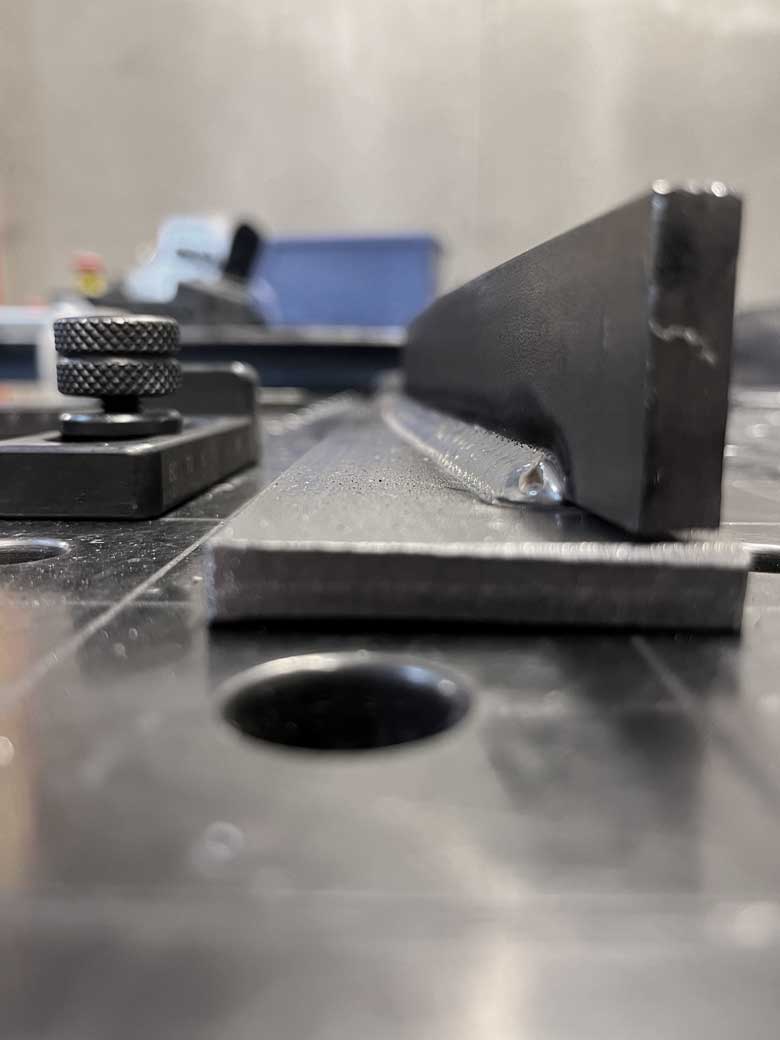
The sentence implies that a robot’s actions are limited by the instructions it receives from its operator.
A robot does not have the ability to think or act on its own, and it can only perform tasks that it has been specifically programmed or instructed to do.
With Seam Tracking, this statement is not entirely true anymore. The CoWelder can actually make small adjustments on how to follow the seam during welding – though it is defined by the user to some degree.
When can you benefit from using Seam Tracking for your CoWelder?
Operating the CoWelder requires thorough introduction to cobot programming, but it is easy to learn and you will quickly get in control. In general, we advice operators to work closely with experienced welders about welding specifications.
You can benefit from cobot welding seam tracking if a weld item changes due to being heated over time.
Some common situations where the seam tracking system is used for cobot welding include:
Welding of complex shapes:
When welding complex shapes, such as curved or irregular surfaces, seam tracking can help the cobot maintain a consistent distance from the workpiece and ensure accurate weld placement.
Welding of thick materials
Welding thick materials can present challenges it creates excessive heat distortion. Seam tracking can help to maintain a consistent weld path and reduce the risk of defects in the finished product.
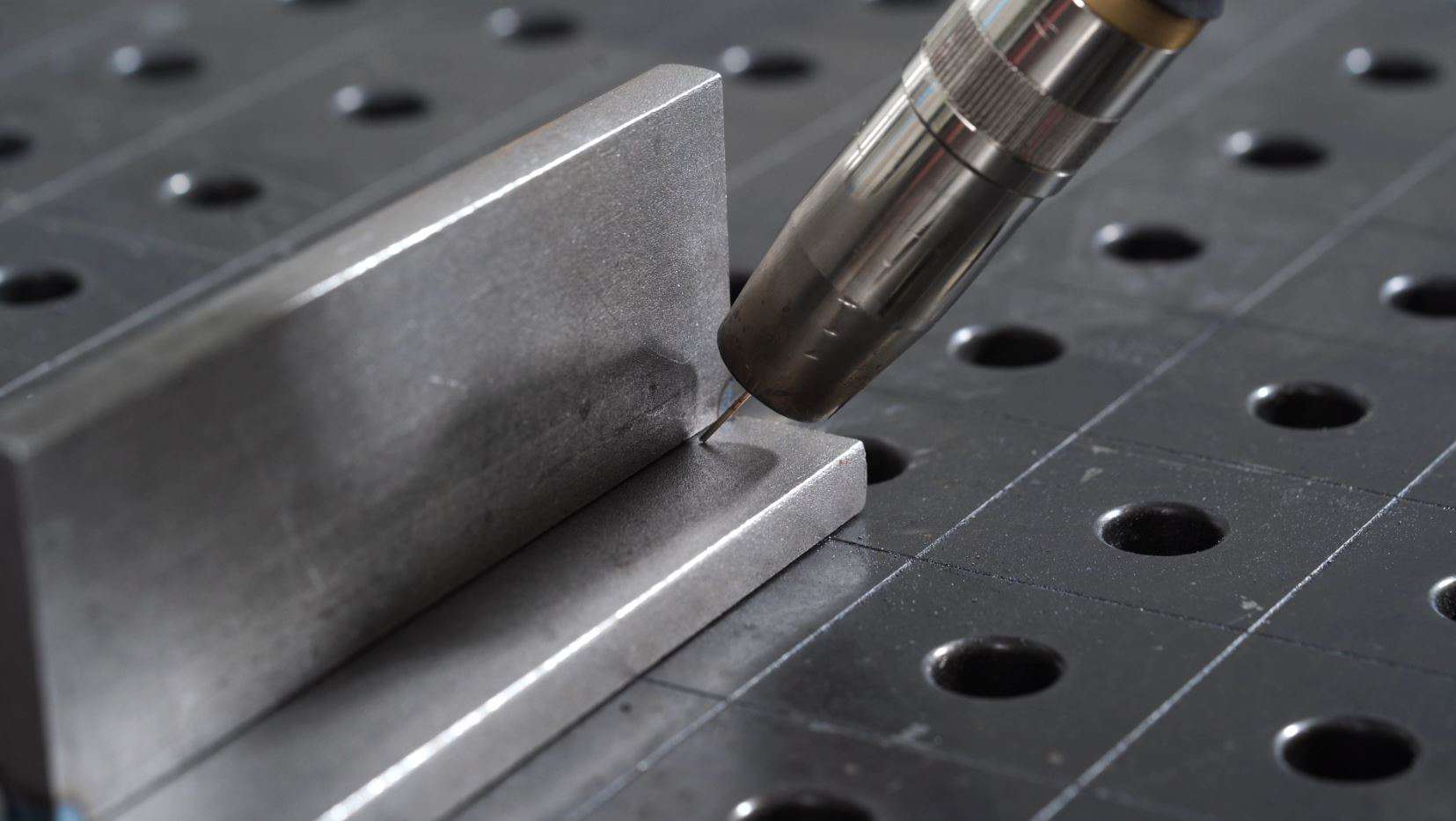
How is Seam Tracking used in Welding Applications?
In practical terms, the technology helps to reduce the need for manual adjustments during welding and in that way save valuable time and improving overall productivity. By automating the process and ensuring greater accuracy, seam tracking can also help to reduce the risk of defects and rework, resulting in higher quality finished products.
In addition, the technology can be used with a wide range of welding processes and materials, making it a versatile solution for production managers looking to streamline their operations.
Combine Seam Tracking and Weaving
Use Seam Tracking and the function Weaving at the same time to optimise the instant tracking.
What is Weaving?
With Weaving, CoWelder makes the torch able to fill a V-seam. The torch makes a zig-zag movement along the joint, and in that way, extends the size of the bead width.
Automated welding with industrial robots
Seam tracking technology is recognised in industrial robotics. Our subsidiary, Migatronic Automation, leads the way in developing automated welding solutions that can be adapted to any requirement – and budget.
With our expertise and focus on innovation, we always aim to deliver solutions that not only enhance productivity but also guarantee the utmost quality and reliability in the welding process. From small-scale production environments and collaborative welding solutions to large industrial facilities, solutions are available as standard or customised to meet particular demands and ensure maximum efficiency and precision.
Compare advantages of different levels of automation when it comes to welding. We can deliver it all.
What is the CoWelder?
The CoWelder is a collaborative welding robot, designed by Migatronic. We have combined the best and latest welding technology with innovative cobot technology from Universal Robots, creating a new category-defining welding solution with broad applications.