Once, a lone welder conquered a mountain of tasks with nothing but his torch and skilled hands.
In days gone by, the workshop resounded with constant clanking, while the air hung thick with fumes, a clear sign of the arduous labour being undertaken.
Yet, we now witness an incredible leap forward, as collaborative welding robots take on the heavy lifting, turning the once noisy and hazardous environment into a relic of the past.
Here’s how you can transform your welding environment for MIG and TIG into a clean, safe and efficient workspace with a collaborative welding robot such as the CoWelder.
Table of Contents
How CoWelder relieves welders
The CoWelder relieves the welders in your production and contributes to a better welding environment. This improves the overall working environment. It carries out all the tiring, repetitive movements that cause muscle fatigue and physical strain. Moreover, welders avoid being exposed to direct radiation and welding fumes.
The CoWelder also helps increase your welders’ motivation and job satisfaction because the robot releases welders for more complex welding assignments. Ultimately, the robot contributes to improving productivity and results.
The CoWelder is not designed to replace manual labour. It optimises work processes in close collaboration with welders.
You know, it is hard to motivate an employee to do the same work for 700 hours. That is not a problem with the CoWelder.
Kuhz Metallbau, Germany
Relieved of exhausting work
Without CoWelder, your welder may get back pains when welding in awkward positions in order to get the work done. Eventually he/she may need sick days and even treatment.
With CoWelder your welder is comfortably watching the CoWelder carrying out the back-busting runs, while the next workpiece is prepared.
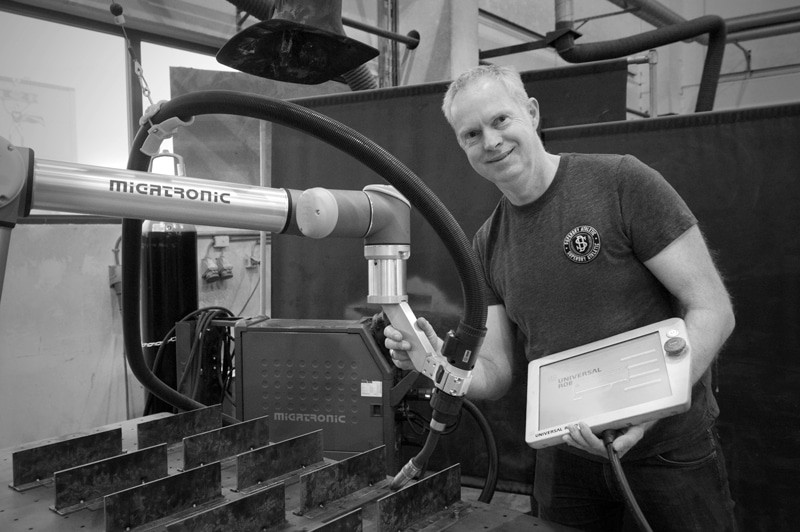
“Welding can be hard work, especially when our welders are working on large batches. These assignments entail similar motions and static positions over long periods of time, which can be quite tough physically. With the CoWelder, our welders are relieved from this kind of work, which has remarkably improved their working environment.”
Smed T. Christiansen, Norway
The welders avoid welding fumes and get a better welding environment
Electric arc welding generates welding fumes and UV radiation. Inhalation of welding fumes can cause short-term discomfort but in the long term, exposure may be harmful to the welder. That is why use of ventilation and respiratory protective equipment is indispensable. However, to simply not be near the weld pool will always be the best way to eliminate the risk of inhaling welding fumes.
Luckily, the CoWelder doesn’t mind.
Enhancing Worker Safety with Cobots
Cobots reduce workplace hazards by undertaking high-risk welding tasks, resulting in reduced exposure to air pollution such as harmful fumes and other gases, decreased noise levels, and a significant decrease in accident potential.
By handling repetitive and physically demanding jobs, cobots alleviate the strain on welders’ bodies, leading to a much healthier workforce.
Regulations regarding safety, noise, and clean air are becoming increasingly stringent, varying from country to country, making it essential to stay ahead. This is where a welding cobot, such as the CoWelder, comes into play. It can improve the welding environment immediately.
Minimising Hazardous Exposure
Cobots weld with precision and consistency, characteristics that decrease the generation of hazardous emissions. In hazardous work zones, cobots represent a surge in safety, significantly reducing workers’ exposure to harmful elements and in that way improve the working environment.
Cobots ensure that welders are not exposed to welding smoke and fumes, guaranteeing a cleaner workspace and healthier air quality.
By mitigating these dangers, cobots protect our workforce, enhance health and productivity in welding environments, and ensure a future with cleaner and safer workflows.
Less Noise Pollution
The workshop’s noisy atmosphere becomes a thing of the past when cobots join the team. Their smooth operation stands in stark contrast to the loud commotion of traditional welding.
From their inception, cobots have been meticulously designed to operate quietly, transforming the acoustic landscape of industrial settings. The reduction in noise pollution not only improves communication clarity but also reduces fatigue among the workforce.
In bustling welding environments, integrating cobots is like turning down the volume. Their compatibility with soundproof enclosures and low-noise equipment helps minimize sound emissions, creating a more focused and peaceful workspace.
Imagine a day where precise automation meets efficient silence. With cobots leading the way, this vision becomes a reality, ushering in an era of serene productivity that enhances the daily experience of every welder.
The impact of cobots on noise reduction in the workshop goes beyond mere pleasantness; it has a profound effect. Silence may be considered golden, but in welding, it also promotes productivity and safety.
Boosting Productivity via Automation
By embracing cobots in the welding environment, not only does the noise level decrease, but operational efficiency also significantly improves.
These agile machines streamline workflow with their precise and reliable performance, freeing human workers from repetitive and physically demanding tasks. This shift leads to a notable increase in productivity, as cobots tirelessly carry out tasks with accuracy, resulting in higher output and consistent weld quality. This is the essence of improving your welding environment.
By assigning repetitive work to cobots, the workforce can redirect their energy towards more complex and value-added activities. This improved allocation of human expertise creates an environment conducive to innovation and strategic thinking, ultimately raising the standard of projects undertaken. Cobots are not just tools; they are partners in progress, reshaping the dynamics of a high-performance welding workspace.
Streamlining Repetitive Tasks
In the realm of metalwork artistry, cobots are the tireless partners who consistently deliver exceptional results. They don’t need breaks and days off – they take over all manual metal arc welding if you will allow it.
- Eliminate Human Fatigue: Cobots tirelessly handle the dull, repetitive tasks allowing welders to focus on complex projects instead.
- Consistent Quality: Automation ensures every weld is uniform, reducing the risk of errors associated with human variability.
- Continuous Operation: Cobots can operate round the clock without breaks, significantly increasing throughput.
- Enhanced Safety: By taking over repetitive tasks, cobots reduce the physical strain on workers, lowering the risk of injury.
Entrust the monotonous to cobots and witness a surge in efficiency and job satisfaction.
With cobots, the rhythm of production never stalls, ensuring a seamless, optimal workflow.
Our motivation for automating the welding process is to prevent the shortage of skilled workers. The efficiency of the CoWelder allows us to release work capacity for other tasks.
Kuhz Metallbau, Germany
Consistent Welding Quality
Achieving consistency in the welding environment is a fundamental aspect of achieving excellence in production. Cobots fulfil this requirement flawlessly, weld after weld.
Since their introduction, cobots have revolutionised the consistency in welding applications within the welding environment. Their programming allows for precise control, ensuring that every weld is as impeccable as the first.
It gives a brilliant and uniform finish that minimises the need for post-treatment. This is very important for us as suppliers to the food industry.
Ole Almeborg, Denmark
Precision combined with repeatability is the winning combination offered by cobots in the welding environment. They replicate the same movements with unwavering accuracy, eliminating human error and enhancing product quality.
Consistent welding quality within the welding environment results in fewer reworks and rejects. Cobots’ precision leads to significant savings in time and materials, which can have a substantial impact on your bottom line.
With cobots at the helm in the welding environment, a high level of weld quality is not just an aspiration—it is guaranteed. Your workforce can rely on this steadfast technology day in and day.
Integrating Cobots for Flexibility
Flexibility in welding operations opens the door to improved efficiency and adaptability, and this is where cobots shine. Easily programmable, they accommodate a wide range of tasks and can switch between applications with minimal downtime. Their design expressly caters to the dynamic needs of a welding environment.
Incorporating cobots into your workflow not only elevates agility but also streamlines production processes. Integration is straightforward, empowering your team with advanced technology while enhancing the adaptiveness of your operations.
We are pleased with the CoWelder because programming components and switching from one component to another is easy – its flexibility is amazing.
L&S Technisher Handel, Germany
Adaptable Welding Stations
Imagine workstations that can easily change to meet demand, with cobots making this a real possibility in today’s welding workplaces. This is an important factor in improving the overall welding environment.
With their versatility, cobots create welding stations that can handle many different tasks. They are programmed to be very precise, so they can do detailed welds and switch between projects smoothly. These robot helpers reduce the time it takes to set up and can quickly adjust to new tasks, which makes production faster.
Also, cobots can adjust to different ways of joining materials and different types of materials. They have special sensors and controls that help them find and move through small differences very accurately, which means the quality of their work stays consistent no matter what.
CoWelder made us think differently about our production processes. We constantly try to find more components for the robot, because it improves the quality and we can finish more in less time.
VM Tarm, Denmark
Lastly, cobot systems are made up of parts that can be changed quickly, so welding stations can be set up differently without much delay. This means they can handle changes in how much work needs to be done, while still keeping the quality high – better welding environment right there.
Cobots are very good at adapting, which means less time when work isn’t getting done and a smoother way of working, which makes your welding business stand out for its excellence.
Real-Time Skill Augmentation
Cobots serve as a force multiplier for welders, injecting expertise and precision into every task.
- Direct Human-Cobot Collaboration: Operatives guide the cobot, enhancing their skill set.
- Instant Feedback Loops: Rapid adjustments to welding parameters improve outcomes.
- Consistent Skill Level: Regardless of welder experience, cobots ensure uniformly high-quality welds.
Cobots elevate the novice welder to expert levels instantly.
Even the most adept welders benefit from the consistency and endurance of cobots.
Streamlining Operations with Cobots
When it comes to efficient and cost-effective production, cobots are the champions. By integrating cobots into your workflow, you can significantly reduce cycle times, leading to faster return on investment (ROI) and lower labour costs.
Foremen overseeing cobot-assisted operations witness a remarkable decrease in wasted time, as cobots work tirelessly with precise accuracy. Welders can spend their time on other tasks, which can improve their motivation as the welding environment is improved.
Taking control of your finances with cobots means embracing a “less is more” approach within the welding environment. Not only do you save time, but you also reduce the need for extensive operator training. This keeps your operations flexible, your expenses low, and your production capabilities running at full speed. The result is a leaner budget that maintains high-quality output and keeps up with market demands.
We have been able to lower the cost price on some of the components that CoWelder makes. It provides the flexibility we need to make it a cost-effective way of automating our production even though our series are small.
VM Tarm, Denmark
In summary, cobots offer a pathway to lean and efficient manufacturing which is also part of the welding environment. By harnessing their capabilities, you can achieve greater productivity, cost savings, and maintain a competitive edge in the industry.
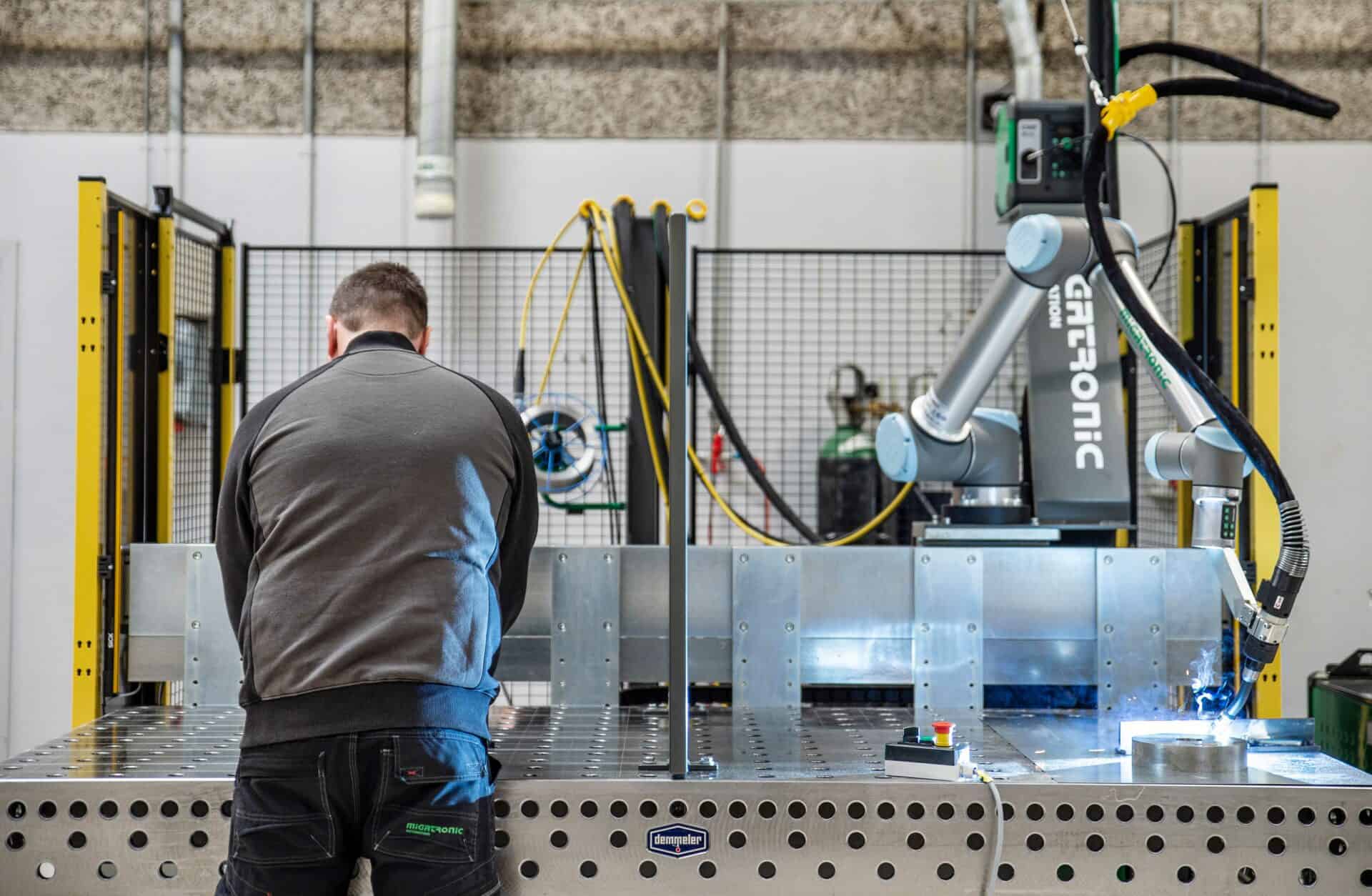
Minimising Material Waste
Being able to control and reduce waste in welding is crucial, and cobots excel in this area.
- Enhanced Accuracy: Cobots are incredibly precise, which means less unnecessary welding and material usage.
- Programmable Repetition: They can consistently perform the same welds without wasting materials.
- Optimised Path Planning: Cobots move efficiently, resulting in less filler and gas waste.
- Material Monitoring: Real-time tracking helps minimise excess inventory and spoilage.
- Predictive Maintenance: Cobots have reduced downtime, preventing material spoilage during unexpected breakdowns.
By strategically using cobots, you can ensure that you measure accurately and minimise waste. Embrace a future where lean manufacturing is not just a goal but a reality in your everyday operations when and improve the welding environment.
Lowering Energy Consumption
Using cobots in welding allows for significant energy savings due to their energy-efficient design and operational capabilities.
Cobots consume less power compared to traditional automated systems. Their precision reduces the need for energy-intensive rework and corrections, resulting in lean and efficient energy usage.
Sophisticated cobots, or rather the welding machine that is part of the solution, offer energy-saving modes that minimise power consumption during standby periods and slow cycles within the welding environment. Additionally, welding cobots’ smaller size and lighter weight require less energy for heating and material handling. This can lead to substantial reductions in energy costs while streamlining operations. Embrace a future where sustainability is integrated into your welding processes.
As a production company, it is important to prioritise and manage energy consumption effectively. In today’s business landscape, more and more companies are focusing on sustainable practices and environmental responsibility, and here, the welding environment is essential.
Many organisations now require their suppliers and partners to meet specific energy consumption criteria as part of their sustainability initiatives, aiming to minimise their environmental impact.
Do you know where to begin?
We can assist you in pinpointing the steps that are most beneficial for your welding production in improving your welding environment.
Drawing from our experience with numerous companies, we can identify initiatives and actions that not only improve energy consumption in welding but also enhance the welding environment for your welders and operators.
What is the CoWelder?
The CoWelder is a collaborative welding robot, designed by Migatronic. We have combined the best and latest welding technology with innovative cobot technology from Universal Robots, creating a new category-defining welding solution with broad applications.