Schon seit der Gründung im Jahr 2011 ist das Unternehmen dynamisch gewachsen. Neben den üblichen Metallkonstruktionen (Balkongitter und Geländer, Treppen, Tore und Zäune) stellt Kuhz auch Bootsanhänger als Sonderanfertigungen her und ist zudem Zulieferer anderer Unternehmen.
Insbesondere die Zunahme des Geschäftes bei Bootsanhängern führt regelmäßig zu Engpässen im Produktionsbetrieb des Unternehmens. Kuhz bietet Anhänger für Motor-, Segel- und Schlauchboote mit einer Nutzlast zwischen 570 und 2870 Kilogramm her. Was Qualität und Ausstattung der Anhänger angeht, betrachtet sich das Unternehmen den bekannten Wettbewerbern auf diesem Markt als ebenbürtig.
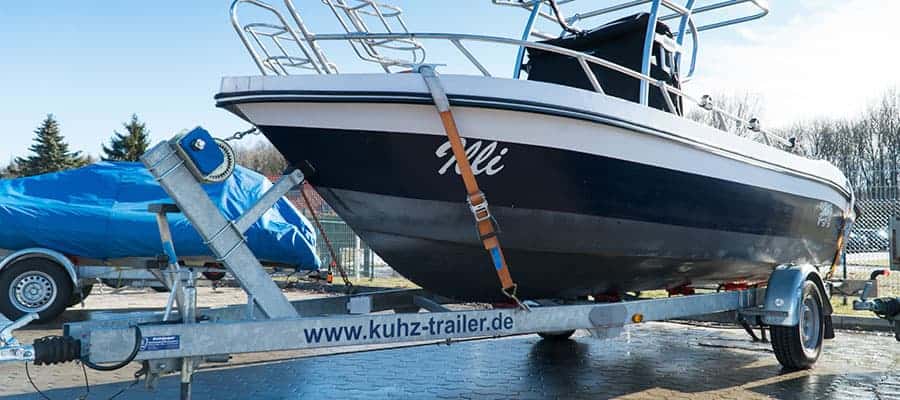
CoWelder: eine flexible und kostengünstige Lösung
Als der Migatronic-Händler SUT Rostock den CoWelder vorstellte, war Roland Kuhz gleich begeistert. Insbesondere für kleine Unternehmen mit Kleinserien zwischen 20 und 300 Werkstücken ist CoWelder eine flexible und kostengünstige Lösung. Nach Lieferung und Inbetriebnahme durch Migatronic und mit einer halbtägigen Einführung konnten die Mitarbeiter bereits erste Komponenten produzieren. Im Rahmen eines zweitägigen Kurses bei Migatronic wurden zwei Mitarbeiter in der Programmierung von CoWelder ausgebildet.
Produktion von Bugstützen für Bootsanhänger
Die Bearbeitungszeit pro Komponente betrug acht bis zehn Minuten. Heute dauert das reine Schweißen weniger als fünf Minuten, und die gesamte Bearbeitung einschließlich von Bestückung und Entnahme sowie Nachbearbeitung dauert für drei Komponenten weniger als zehn Minuten. So konnten wir die durchschnittliche Bearbeitungsdauer pro Komponente auf etwas über drei Minuten verkürzen. Die erheblichen Kostenvorteile durch die kürzere Produktionszeit kommen gut gelegen.
“Unser Grund für die Automatisierung des Schweißverfahrens ist die Sorge vor einem Mangel an Fachkräften. Die Effizienz von CoWelder ermöglicht es uns, Kapazitäten für andere Aufgaben freizustellen. CoWelder ist jetzt seit sieben Monaten in Betrieb. Inzwischen haben wir einen Fertigungsauftrag übernommen, an den früher nicht einmal zu denken war, nämlich 1200 Schweißpositionen an 600 Komponenten. Dank CoWelder haben wir uns darangetraut. Und man kann keinem Beschäftigten zumuten, 700 Stunden lang dieselbe Arbeit zu machen. Für CoWelder ist das kein Problem.” – Roland Kuhz
Ösen für schwere Schiffsbauteile
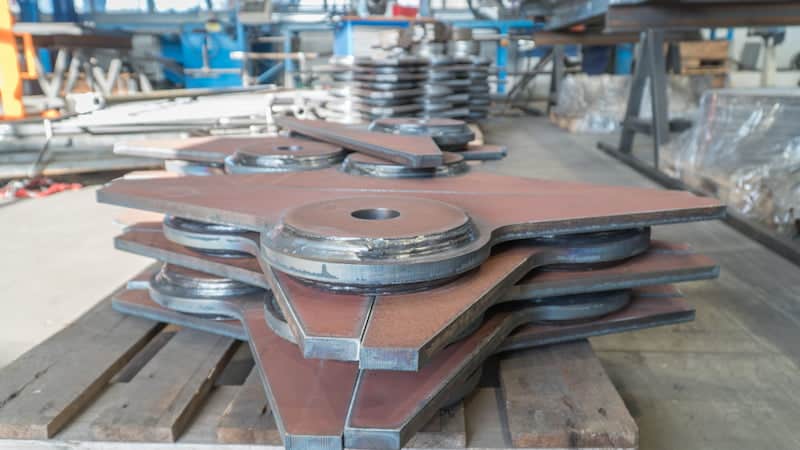
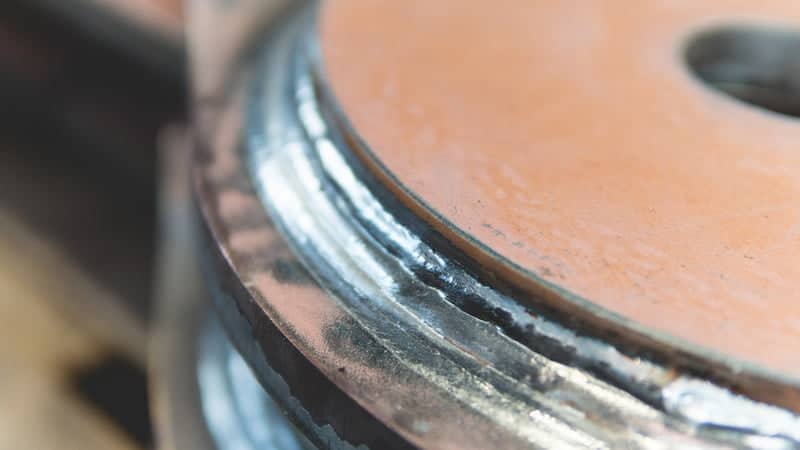

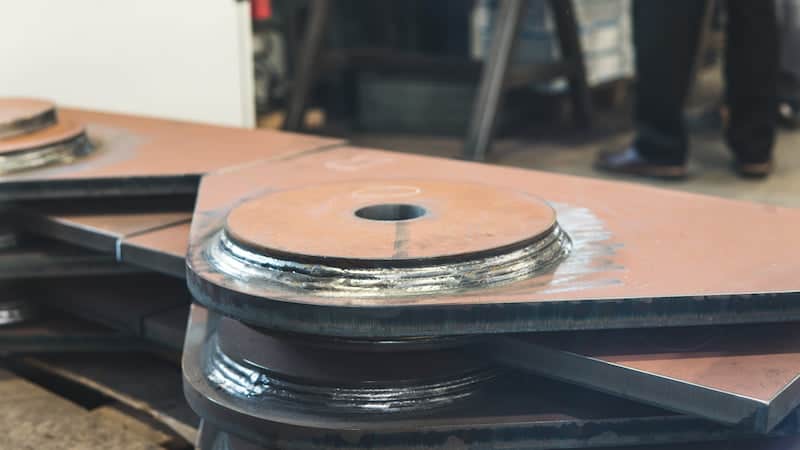
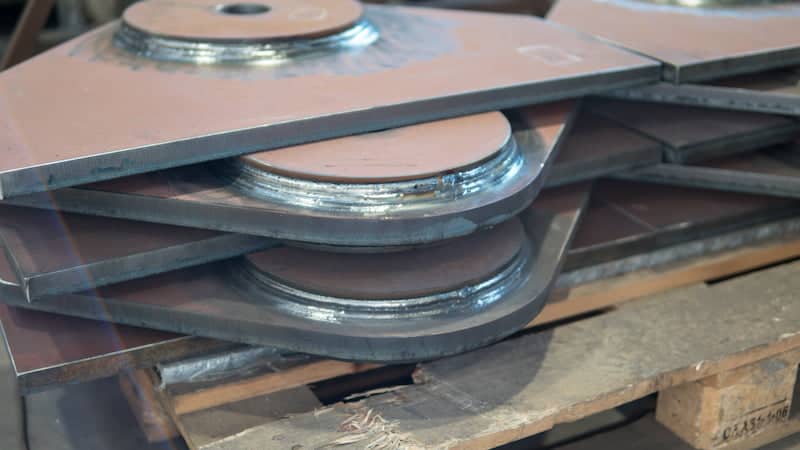
Bei diesem Auftrag werden Ösen für Schiffsbauteile hergestellt, die bis zu 300 Tonnen wiegen. Es werden 30 mm dicke runde Bleche auf 30 mm dicke Stahlplatten geschweißt. Nach dem Schweißen einer Wurzellage werden auf beiden Seiten des Bauteiles vier weitere Schweißnähte ausgeführt. So entstehen auf jeder einzelnen Komponente etwa zehn Meter geschweißte Rundnaht. Bei manueller Fertigung würde die Dauer pro Komponente 70 Minuten betragen. Mit CoWelder dauert die Bearbeitung 30 Minuten, und die Zeitdauer zum Drehen des Bauteiles ist darin bereits inbegriffen. Für die Herstellung von 600 Komponenten werden 30 t Stahl bearbeitet.
Die Schweißer können sich um anderes kümmern
Ein Schweißer benötigt rund 700 Stunden, also 17,5 Arbeitswochen, für die Herstellung der Komponenten. Gemeinsam mit CoWelder braucht der Schweißer nur noch wenige Minuten dafür, die Komponenten einzuspannen und zu übergeben. Den größten Teil der Zeit kann der Schweißer dann mit anderen Aufgaben verbringen.
Erzeugt einheitliche Qualität
Erwähnt werden muss die Qualität der Schweißnähte von CoWelder: Anders als beim Schweißen von Hand stellt CoWelder Rundnähte durchgehend, also ohne Unterbrechung, her und erreicht damit eine deutlich höhere Qualität. Hinzu kommt noch die Ausdauer des Roboters. „Egal ob in der Tag- oder in der Nachtschicht, CoWelder erzeugt stets hochwertige Schweißungen. Von einem Mitarbeiter könnten wir dies niemals fordern“, sagt Roland Kuhz.
Die vorbereitenden Arbeiten, damit der CoWelder diese Komponenten bearbeiten kann, waren wirklich sehr übersichtlich: Es musste eine eher simple Aufspannvorrichtung hergestellt werden, was ungefähr eine halbe Stunde dauerte. Das Einrichten der Schweißprogramme dauerte drei Stunden. Ein lohnend investierter Aufwand, wenn man sich die großen Einsparungen an Zeit und Kosten anschaut.
Vollständiger Einsatz von CoWelder erhöht die Einsparungen.
Neben den erwähnten Produkten werden auch andere Anhängerteile wie Knotenbleche und Rollenböcke mit CoWelder hergestellt. Der Roboter ist im Vollschichtbetrieb gänzlich ausgelastet. Befestigungen und weitere Komponenten werden sukzessive vorbereitet, sodass sich die Kapazitäten des CoWelder ganzjährig für Standard- sowie für Kommissionsbauteile nutzen lassen. Bei rund 15 Anhängerkomponenten rechnet Roland Kuhz mit einer Zeitersparnis von etwa 40 %. Dies bedeutet, dass die Arbeit von 480 Stunden bei händischem Schweißen vom CoWelder in 270 Stunden erledigt wird. Den größten Teil dieser Zeit kann der Schweißer dann mit anderen Aufgaben verbringen.
“CoWelder erleichtert die Arbeit. Die Investition macht sich selbst bezahlt, und wir bereuen natürlich nichts.” – Roland Kuhz