W 2016 roku L&S Technischer Handel GmbH odnotowała wzrost liczby zamówień. Nieustannie wysokie wykorzystanie zdolności produkcyjnej spowodowało ogromną presję i wydłużyło czas dostawy, a także uświadomiło dyrektorowi generalnemu Torstenowi Leziusowi, że coś trzeba zmienić. Inwestycja w rozwiązanie CoWelder umożliwiła firmie produkcję na zamówienie, a nie na stan magazynowy. L&S produkuje raczej niewielkie partie po 50-800 sztuk w różnych wariantach, co wiązałoby się ze znacznymi kosztami związanymi z czasem i zasobami programisty na zaprogramowanie i zmianę tradycyjnego zautomatyzowanego rozwiązania. W związku z tym lokalny dealer sprzętu spawalniczego L&S polecił rozwiązanie CoWelder i zademonstrował jego ogromną elastyczność.
“Jesteśmy zadowoleni z CoWelder, ponieważ programowanie komponentów i przełączanie z jednego komponentu na drugi jest łatwe – jego elastyczność jest niesamowita.” – Torsten Lezius, CEO at L&S Technischer Handel
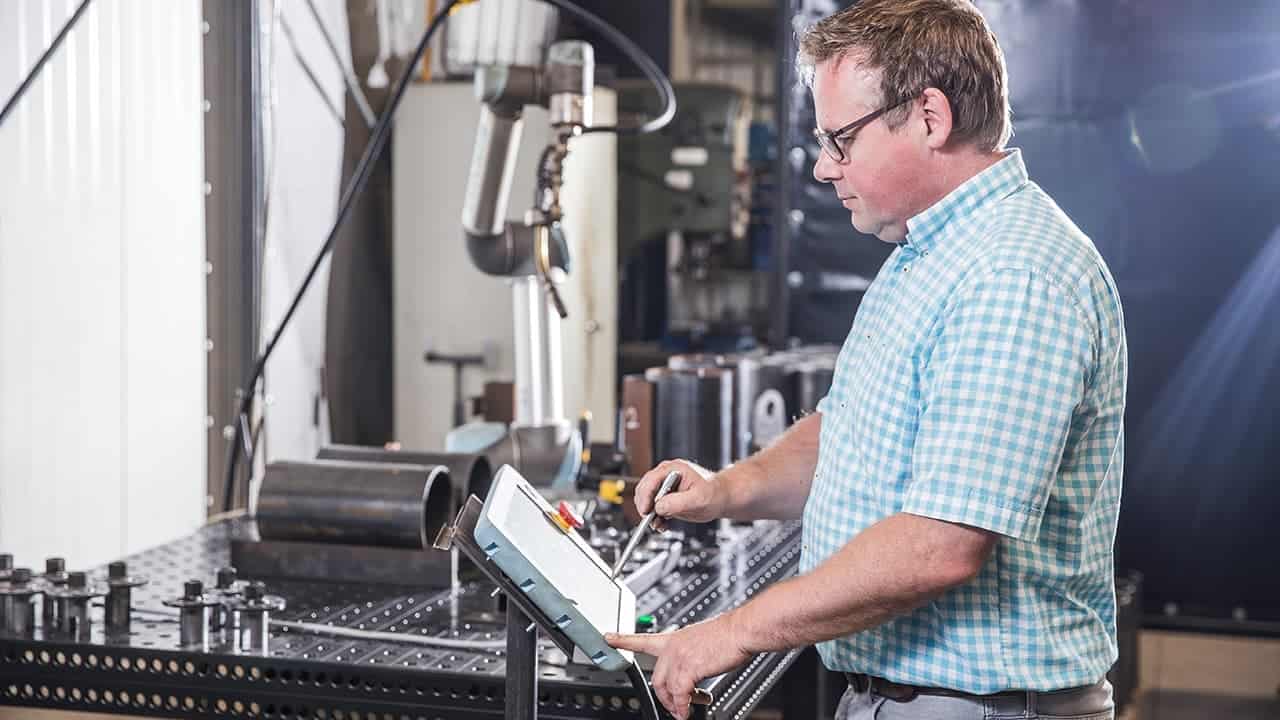
Elastyczność przekracza oczekiwania
L&S produkuje części zamienne do różnych rodzajów pojemników na odpady, pojemników typu roll-off i pojemników ASP. Dzięki licznym produktom końcowym, asortyment produktów z biegiem lat bardzo się powiększył Ze względu na nieregularność zamówień ze strony klientów nie jest możliwe przechowywanie wszystkich części zamiennych na magazynie. Rzadziej sprzedawane komponenty są produkowane na zamówienie, co wymaga dodatkowej elastyczności ze strony personelu spawalniczego. Ponieważ komponenty te są zazwyczaj narażone na ogromne obciążenia, spoiny muszą być wysokiej jakości. L&S miał rzecz jasna podobne wysokie oczekiwania wobec rozwiązania CoWelder.
CoWelder spawa sześć elementów w 10 minut
Jeśli nie ma pilnych zamówień do realizacji, robot zazwyczaj wytwarza dwie jednostki komponentu na raz, na trzech stanowiskach komponentów na stole spawalniczym, co daje w sumie 6 komponentów. Taka rotacja trwa około dziesięciu minut wraz z przygotowaniem osprzętu (uchwytów), w zależności od rodzaju i wielkości. Po przygotowaniu programu dla komponentu programy są losowo łączone i przywoływane za pomocą kilku kliknięć na ekranie dotykowym robota. W ten sposób komponenty są mieszane losowo i można przełączać się między typami oraz kolejnością produkowanych komponentów. CoWelder ma duże moce produkcyjne. Nawet przy zachowawczych szacunkach 5,5 cykli (zamiast 6) na godzinę, ma zdolność do wytwarzania 264 złożonych komponentów dziennie.
“Ponownie rozpoczęliśmy produkcję na stan magazynowy. Niegdyś produkcja tej samej wielkości zajmowała niemal dwukrotnie więcej czasu. W przypadku niektórych komponentów jesteśmy w stanie skrócić czas dostawy z dwóch tygodni do jednego. I z przyjemnością możemy stwierdzić, że nie obciąża to naszych wysoko wykwalifikowanych spawaczy. Komponenty leżą gotowe wieczorem, niczym za dotknięciem czarodziejskiej różdżki.” – Torsten Lezius.
Obsługa robota jest prosta
Obsługą CoWelder, tj. umieszczaniem elementów w oprzyrządowaniu, uruchamianiem spawania, a następnie demontażem komponentów zajmuje się zazwyczaj personel obsługujący przecinarkę, która znajduje się w pobliżu. Każdy czas oczekiwania przy przecinarce można optymalnie wykorzystać, obsługując CoWelder™. Programowaniem i ustawianiem systemu zajmuje się Torsten Lezius lub technik. Po ustawieniu procesu i bezbłędnym zespawaniu pierwszych komponentów swoje zadanie wykonują operatorzy przecinarki. Potrzebują tylko szybkich i prostych wskazówek dotyczących bezpieczeństwa i obsługi CoWelder. W ten sposób optymalne wykorzystanie czasu minimalizuje koszty płac i poprawia wydajność. Pracownicy bardzo pozytywnie przyjęli nowego „kolegę”, co ułatwiło wprowadzenie CoWeldera do codziennej pracy. Nigdy nie postrzegali robota jako rywala i od pierwszego dnia używali go do wykonywania zadań wcześniej uważanych za żmudne. Torsten Lezius był zaskoczony kreatywnymi umiejętnościami swoich pracowników i ich zdolnością do znajdowania sposobów na szybszą, lepszą i tańszą produkcję dodatkowych komponentów za pomocą CoWelder.
The mounts are easy to place in the fixture which accommodates ten mounts in two rows. Welding four mounts takes around 1.10 minutes. Roller holders for containers are also produced in different sizes. On each roller holder there are twelve fillet welds, eight of which are in a downward position. Welding time from beginning the first weld to finalising the last weld has been reduced from approx. 5 minutes to 2 minutes and 27 seconds. Moving the component on the welding table used to be very time-consuming. L&S produce steel containers in different sizes (length, inside and outside diameters) and in batches of several hundred. On each side of the component, the axle bushings are welded with two circular fillet welds. Semiautomatic production with CoWelder has clearly improved both production speed and welding quality.