Under 2016 såg L&S Technischer Handel GmbH en ökad orderingång. Det konstant höga utnyttjandegraden av produktionskapaciteten ledde till ett enormt tryck och längre leveranstid. Det fick VD Torsten Lezius att inse att något behövde göras. Med investeringen i en CoWelder-lösning kunde företaget producera på beställning, istället för att tillverka för lagret. L&S tillverkar ganska små partier (50–800 enheter) och i olika varianter. Det skulle innebära betydande tid- och resursåtgång för en programmerare att programmera och ändra en traditionell automatiserad lösning. Därför uppmärksammade L&S lokala återförsäljare av svetsutrustning företaget på, och demonstrerade, den enorma flexibiliteten för CoWelder-lösningen.
“Vi är nöjda med CoWelder eftersom det är enkelt att programmera komponenter och byta från en komponent till en annan – flexibiliteten är fantastisk” – Torsten Lezius, CEO på L&S Technischer Handel
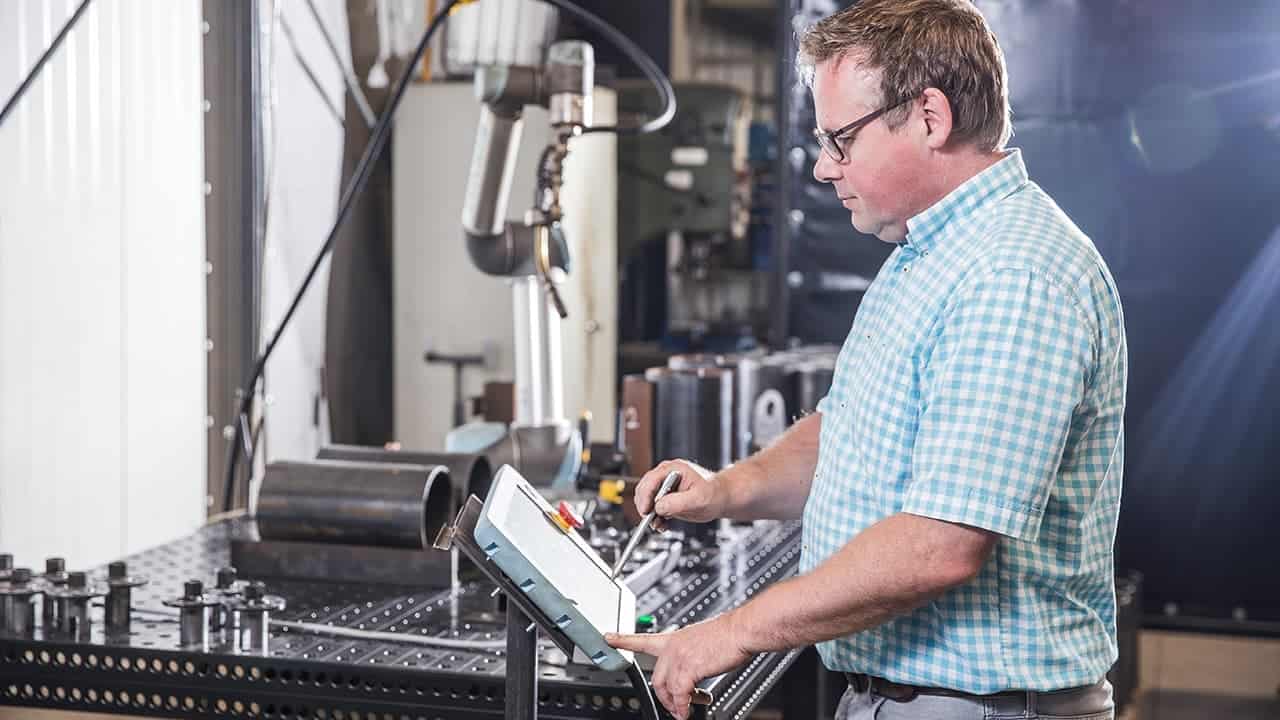
Flexibilitet som överträffar förväntningarna
L&S tillverkar reservdelar till många olika typer av avfallsbehållare, rullflakscontainrar och ASP-behållare. På grund av företagets många slutprodukter har produktsortimentet vuxit enormt under åren.
Eftersom kunderna beställer väldigt oregelbundet går det inte att ha alla reservdelar i lager. Ovanligare komponenter tillverkas på beställning, vilket kräver extra flexibilitet för svetspersonalen. Eftersom dessa komponenter vanligtvis utsätts för enorma belastningar, måste svetsfogarna hålla hög kvalitet. Och naturligtvis hade L&S höga förväntningar också på CoWelder-lösningen.
CoWelder svetsar sex komponenter på 10 minuter
Om CoWelder inte är upptagen med brådskande jobb, tillverkar roboten vanligtvis två av varje komponent samtidigt på svetsbordets tre komponentstationer, vilket ger totalt sex komponenter. Längden för den här typen av rotation är cirka 10 minuter, inklusive förberedelse av fixturer (men det varierar beroende på typ och storlek).
När ett program för en komponent har förberetts, kan olika program kombineras slumpmässigt och hämtas fram med några klick på robotens pekskärm. På så sätt blandas komponenterna slumpmässigt och man kan växla mellan de olika typerna och ordningen för producerade komponenter.
CoWelder har stor produktionskapacitet. Även om man räknar försiktigt med endast 5,5 cykler (istället för 6) per timma, har den kapacitet att producera 264 komplexa komponenter per dag.
“Vi har börjat producera för lager igen. Det brukade ta minst dubbelt så lång tid för samma produktionsvolym. För vissa komponenter kan vi korta leveranstiden från två veckor till en vecka. Och det fina är att våra skickliga svetsare i princip inte har behövt påverkas negativt av detta. Komponenterna ligger färdiga på kvällen – rena magin.” – Torsten Lezius.
Roboten är enkel att använda
Att använda CoWelder, dvs. placera komponenter i fixturer, starta svetsningen och därefter ta bort komponenterna, hanteras vanligtvis av personal som arbetar med en såg i närheten.
Eventuell väntetid vid sågen kan utnyttjas optimalt genom användning av CoWelder™. Programmering och konfiguration av systemet hanteras av Torsten Lezius eller en tekniker.
När processen har konfigurerats och de första felfria komponenterna har svetsats tar sågoperatörerna över. De behöver bara en kort och enkel vägledning i säkerhet och hur man använder CoWelder. Det optimala tidsutnyttjandet ger minimala lönekostnader och ökad produktivitet.
De anställda hade en mycket positiv inställning till sin nya ”kollega”, vilket gjorde att det var mycket enkelt att introducera CoWelder i deras dagliga arbete. De såg aldrig roboten som en rival, utan använde den från dag ett för att utföra uppgifter som tidigare var mycket enformiga.
Torsten Lezius blev förvånad över sina anställdas kreativitet och deras förmåga att hitta andra komponenter som kunde produceras snabbare, bättre och billigare med CoWelder.
The mounts are easy to place in the fixture which accommodates ten mounts in two rows. Welding four mounts takes around 1.10 minutes. Roller holders for containers are also produced in different sizes. On each roller holder there are twelve fillet welds, eight of which are in a downward position. Welding time from beginning the first weld to finalising the last weld has been reduced from approx. 5 minutes to 2 minutes and 27 seconds. Moving the component on the welding table used to be very time-consuming. L&S produce steel containers in different sizes (length, inside and outside diameters) and in batches of several hundred. On each side of the component, the axle bushings are welded with two circular fillet welds. Semiautomatic production with CoWelder has clearly improved both production speed and welding quality.