Ein Tanklastwagen besteht aus vielen verschiedenen geschweißten Komponenten. Wenn viele davon Standardkomponenten sind, ist die Verarbeitung während der gesamten Produktion einfacher und schneller – vom Konstruktionsbüro bis zum fertigen Tanklastwagen.
Als VM Tarm die CoWelder in die Produktion integrierte, mussten sie ihre bestehenden geschweißten Teile auf eine neue Art betrachten. Sie stellten fest, dass es durch das Umgestalten einiger Komponenten möglich war, die Auswahl an Standardkomponenten zu erweitern, sodass noch mehr davon zu ihrem neuen CoWelder passen würden.
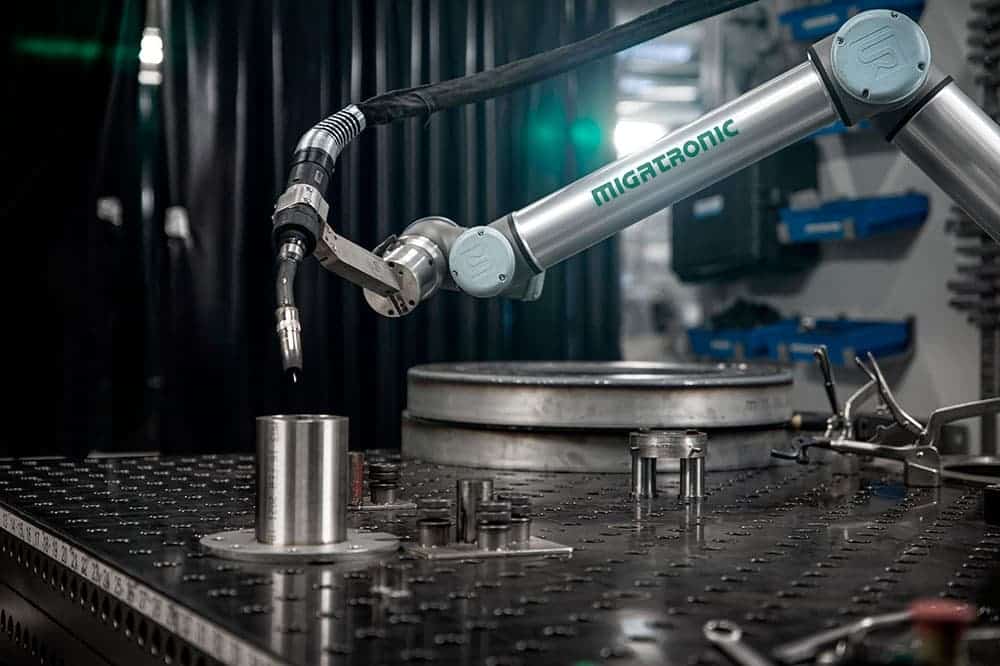
CoWelder schafft auf vier Arten Wert für VM Tarm
1. CoWelder spart täglich 4 Stunden Lichtbogenschweißzeit
Die meisten Komponenten sind ziemlich groß mit viel Lichtbogenschweißzeit. Der Roboter schweißt täglich etwa 4 Stunden. In der Zwischenzeit kann der Bediener andere Aufgaben erledigen. Meistens bereitet er die nächsten Komponenten durch Heftschweißen ihrer Unterteile vor.
„Ich habe jetzt zwei Arbeitsstationen. Eine für den CoWelder und eine für das Heftschweißen. Ich gehe jeden Tag mehrmals hin und her. Wir können mehr Komponenten fertigstellen, indem wir die Arbeit zwischen mir und dem Roboter aufteilen.“ – Teddy Bregnholm, Roboterbediener
2. Flexibilität macht die Produktion kosteneffizient
Das Management erkennt, dass ihr CoWelder unendliche Möglichkeiten zum Schweißen aller Arten von Komponenten bietet. Die Flexibilität der Lösung ermöglicht es ihnen, die Kapazität zu erhöhen, wenn sie es benötigen.
„Wir konnten den Stückkostenpreis für einige der Komponenten, die CoWelder herstellt, senken. Es bietet die Flexibilität, die wir benötigen, um es zu einer kosteneffektiven Art der Automatisierung unserer Produktion zu machen, auch wenn unsere Produktionsserien klein sind.“ – Karsten Lauridsen, Produktionsleiter
3. Hohe Wiederholgenauigkeit und niedrige Fehlerquote
Der CoWelder schweißt etwa 100+ verschiedene Komponenten, einige sehr oft und andere sehr selten. Egal was, sie sind jedes Mal komplett identisch und die Fehlerquote ist gering.
„Wir stanzen, biegen und schneiden unsere Unterteile selbst, damit wir sicher sein können, dass sie immer zusammenpassen. Deshalb können wir den CoWelder ohne zu zögern schweißen lassen und sicher sein, dass die Komponenten jedes Mal vollkommen gleich sind.“ – Lars Pedersen, Vorarbeiter
4. Zur Arbeit zu gehen macht jetzt mehr Spaß
Der Bediener schweißt nicht mehr von Hand die großen Komponenten. Heute ist er frei von den routinemäßigen Schweißarbeiten, die er zu fürchten begonnen hatte. Außerdem ist er weniger Schweißrauch und unangenehmen Arbeitspositionen ausgesetzt. Er gibt ehrlich zu, dass er, seit er mit dem CoWelder arbeitet, jeden Tag eine neu entdeckte echte Freude verspürt, zur Arbeit zu gehen.
„Ich habe viele Jahre als Schweißer gearbeitet und irgendwann wurde mein Job eintönig. Es war zu viel des Gleichen. Deshalb war es für mich eine interessante Herausforderung, in das CoWelder-Projekt einbezogen zu werden. Es ist sicher zu sagen, dass die Arbeit mit dem CoWelder mir geholfen hat, wiederzuentdecken, wie viel Spaß Arbeit machen kann.“ – Teddy Bregnholm, Roboterbediener
Die betriebliche Perspektive
Kleine Chargen, große Komponenten
Alle Chargen sind klein, aber die meisten Komponenten sind ziemlich groß. Es gibt entweder viele Schweißnähte oder ein paar lange Schweißungen an einer Komponente. Dies gibt dem Bediener viel Zeit, andere Aufgaben zu erledigen, wie zum Beispiel die Vorbereitung der nächsten Komponenten. Einige Komponenten bestehen aus bis zu acht verschiedenen Programmen auf dem CoWelder.
„Alle Programme im CoWelder sind nach einer Artikelnummer benannt, die unseren Komponenten entspricht. Das macht es einfach, spezifische Programme zu finden und das Werkzeug richtig zu platzieren. Dieses Verfahren minimiert unser Fehlerrisiko“ – Teddy Bregnholm, Roboterbediener.
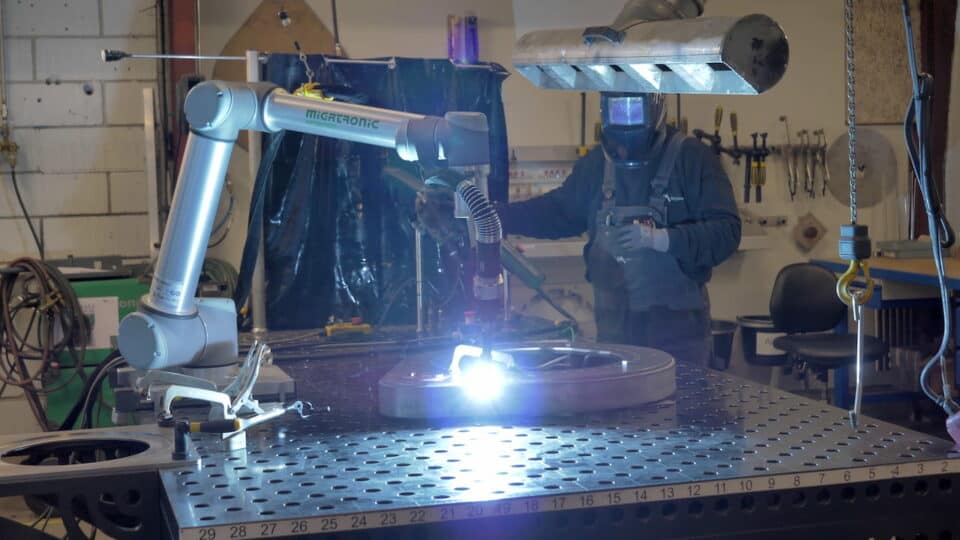
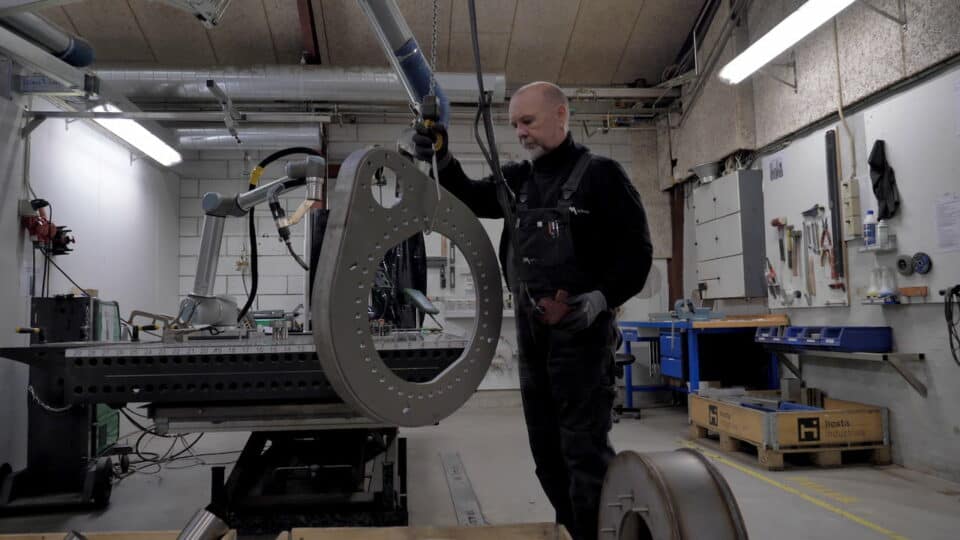
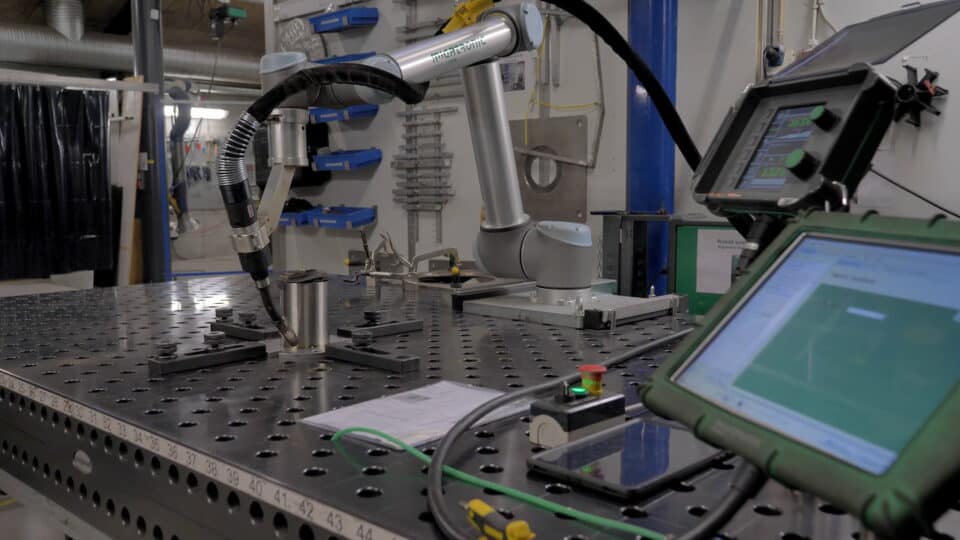
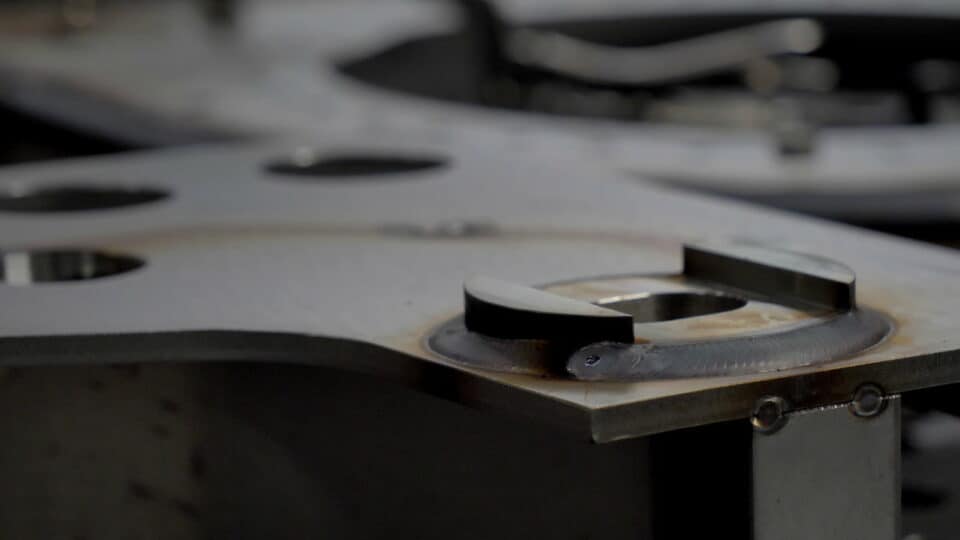
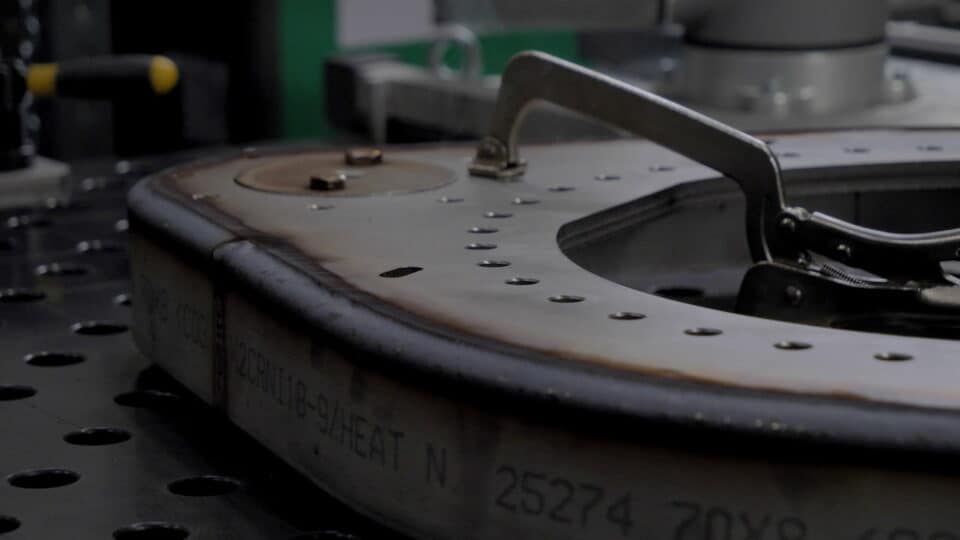
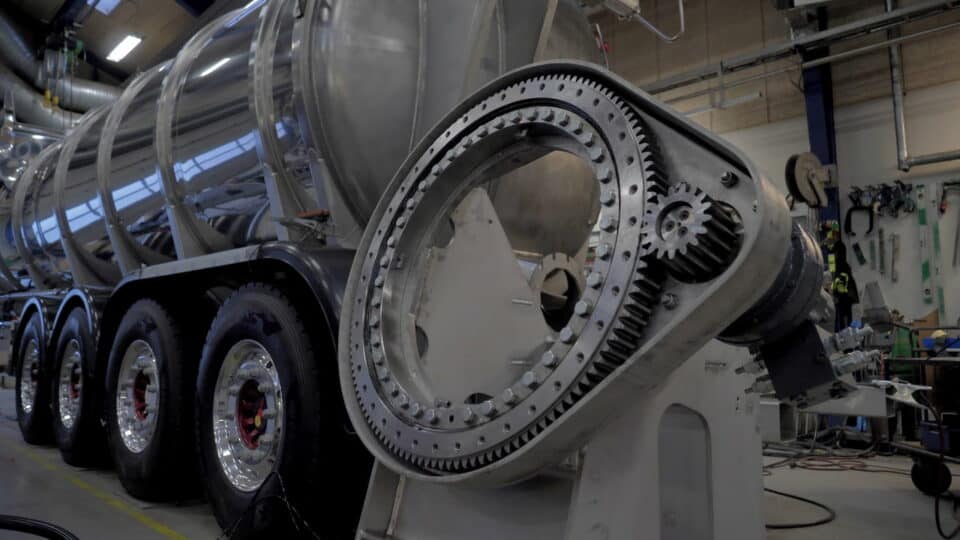
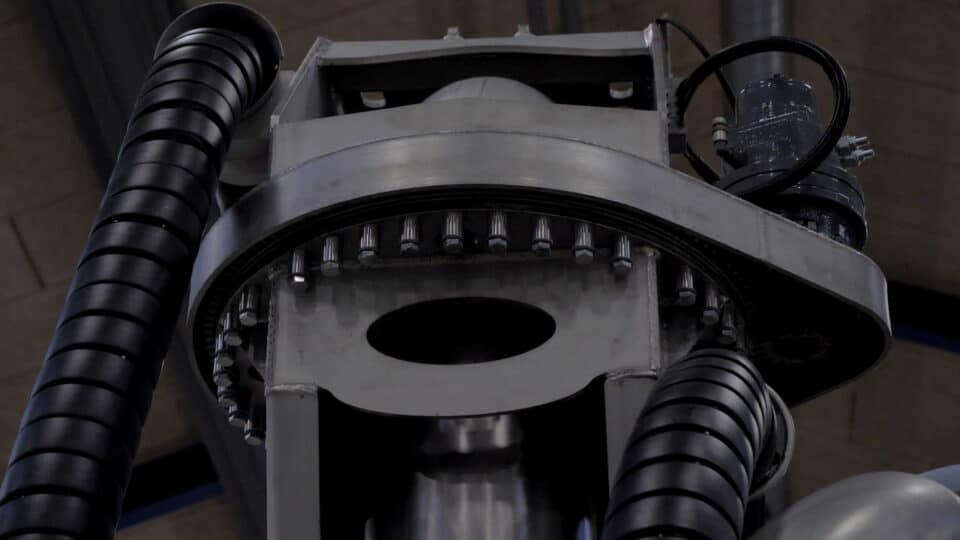
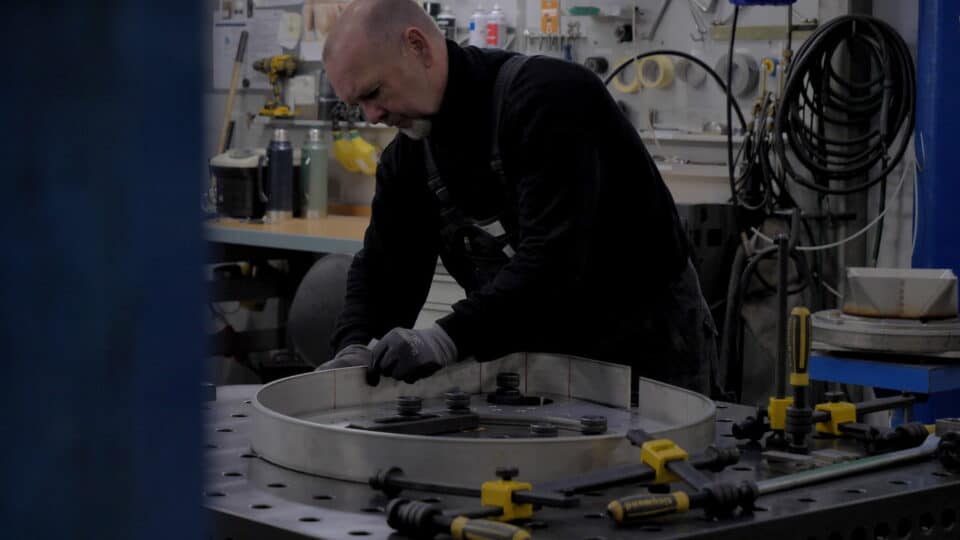