Urban furniture manufacturer HITSA needed enough hands to support future growth. The solution? A CoWelder Track from Migatronic, which has increased productivity by more than 70 percent while significantly improving the working environment.
It’s busy at HITSA in Kolding, which develops and produces benches, bins, bollards and other urban furniture and cycling products for customers at home and abroad.
To accommodate current and future growth, HITSA began exploring options to increase production capacity. However, they soon realized that it was difficult to find enough qualified welding specialists. Instead, the company looked towards increasing automation and in their search found the Migatronic collaborative welding robot, CoWelder.
The choice fell on a CoWelder Track with an integrated, six-meter-long track that allows the welding robot to move sideways along the welding table. The table is also divided into two workstations using a partition wall. This allows the robot to weld on one workpiece while the operator prepares the next.
“We chose to invest in a CoWelder Track because we saw good opportunities to increase our capacity and improve the working environment in our welding department. And the robot has certainly not disappointed. Not least because the welding properties are also top notch, so the quality has also received a boost,” says Production Manager at HITSA, Karina Clemmensen.
23 diverse welding tasks
HITSA offers standard products, but also has the skills to design, produce and install customized solutions. For this reason, the company’s product portfolio is wide-ranging, and the same goes for welding tasks.
CoWelder was initially intended for welding large series with many similar parts, large and small. However, this meant that the robot stood still when it came to producing customized solutions. Therefore, HITSA started testing the welding robot on smaller series, and it turned out to be a good idea.
“When it had been in production for three months, we had programmed the first 23 different welding programs on it. On those jobs, it had improved efficiency by up to 70 percent, so you have to say that it has made a significant difference in our welding production,” says Karina Clemmensen and adds:
“CoWelder is easy to program and operate. This makes it incredibly flexible, so it’s worthwhile for us to use it to weld small series as well. And once we have created a welding program, we can just save it for the next time a customer asks us to produce that solution“
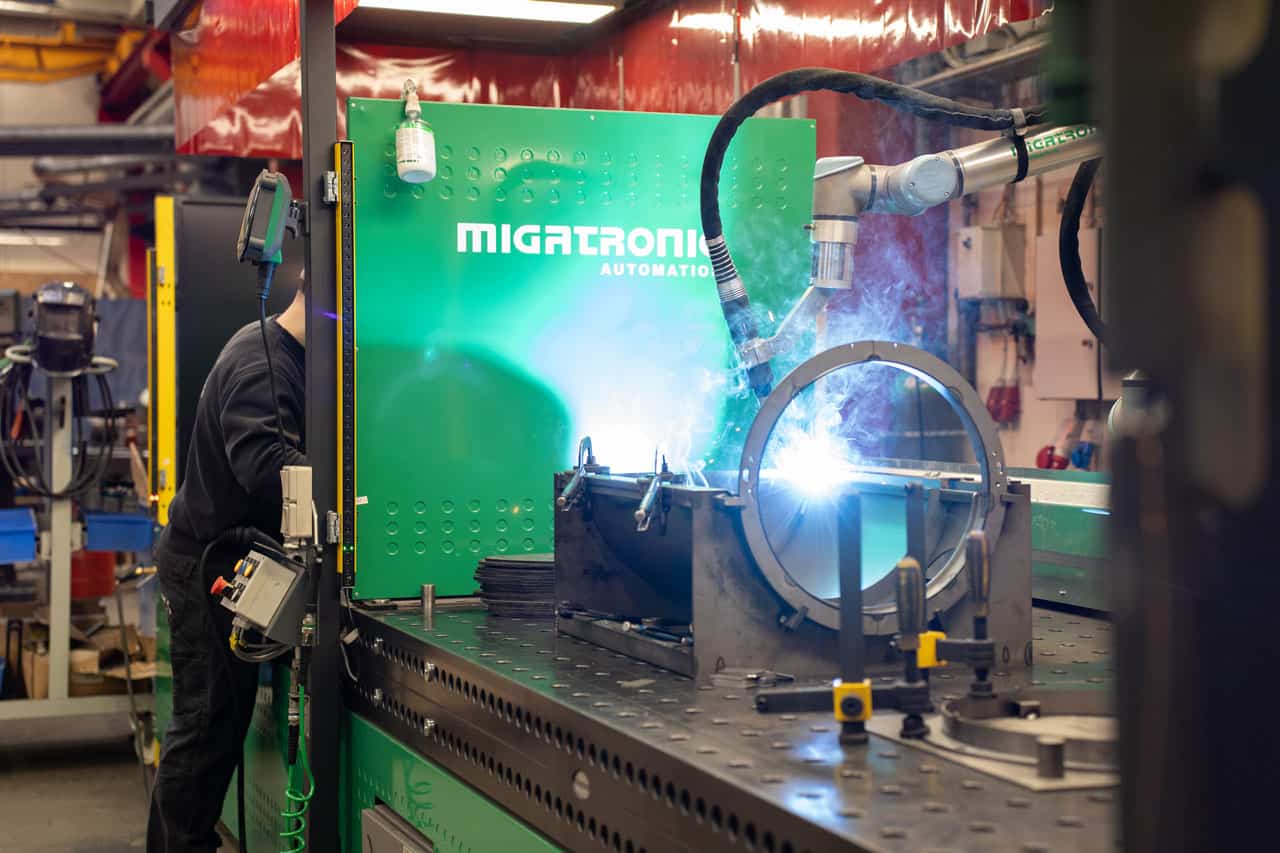
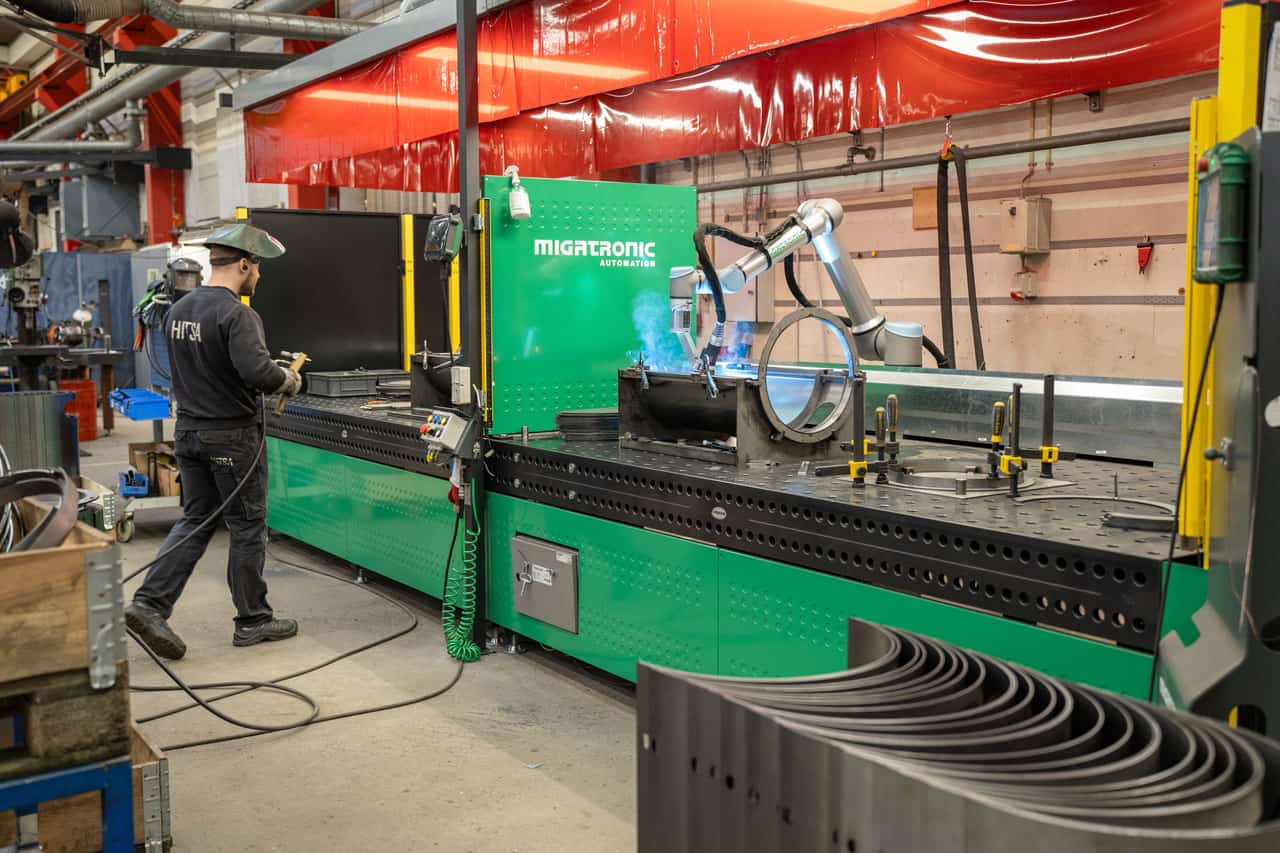
Robot colleague improves the work environment
It’s not just quality and efficiency that CoWelder has made a difference at HITSA. By taking over monotonous tasks or tasks that require the welding specialist to go into demanding working positions, it has also improved the working environment in the company’s welding department.
“CoWelder has taken over the more strenuous and monotonous tasks. This has significantly improved the working environment, especially because our welding specialists can now mainly focus on tasks with better ergonomics. In addition, the welding robot has also freed up time for our welding specialists, who can now focus on other, more specialized tasks. It’s a win-win situation,” says Karina Clemmensen.
HITSA quickly realized the great potential of the welding robot. So the company ordered a second CoWelder Track, this time equipped with specially designed fixtures and a customized turntable that allows the robot to rotate the workpiece during welding. In this way, HITSA will be able to run and test new welding programs on one CoWelder while the other is in full production.

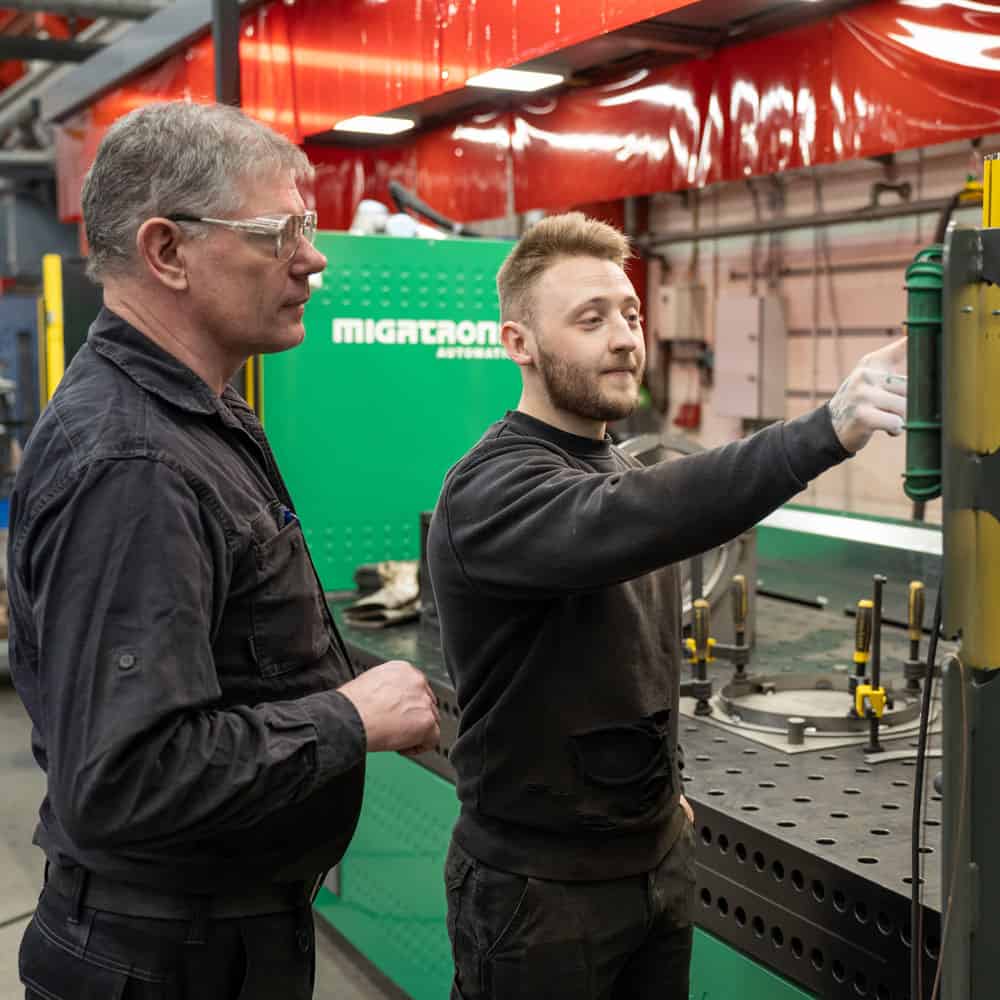